Continuous Catalyst Regeneration
Application Discussion
AD129
June 15, 2003
The Continuous Catalyst Regeneration (CCR) process is part of a process used in the petroleum and petrochemical industries, which produces aromatics from naphthenes and parafins commonly used as motor fuel. In this process (Figure 1), hydrotreated naptha is combined with recycle hydrogen gas, heated to the desired reaction temperature (925 – 975 deg F) and sent through a series of reactors (vertical or side by side). Because the reaction is endothermic, interstage heaters are required between each reactor section to attain the required reaction temperature. In order to attain the desired reactions and high product yield, a metal catalyst such as platinum is used. The catalyst moves from reactor to reactor and the feed mixture flows radially across the catalyst beds.
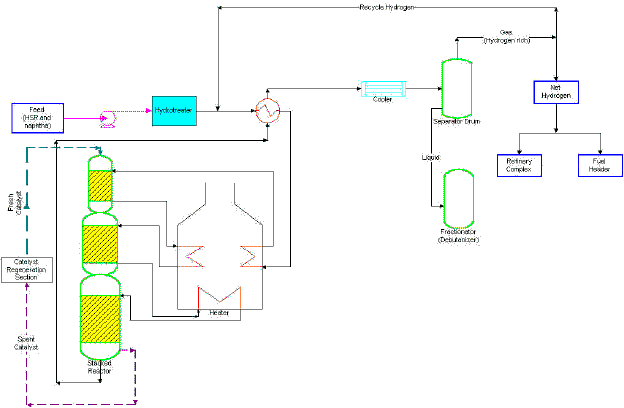
Figure 1: CCR Process with Vertical Reactor Arrangement
The effluent from the last reactor is cooled and split into vapor and liquid phases in a separator. In the separator, hydrogen rich gases are split with some portion being compressed and the rest recycled back to the reactors. The liquid product from the separator is sent to a fractionalization tower where light saturates are removed from aromatic products.
As previously stated, an external catalyst is required to attain the desired product yields. As the reactions occur over time, coke builds up on the catalyst thus reducing its catalytic capabilities. In order to attain the longest life from the catalyst, the catalyst must be regenerated. Regeneration restores the catalyst to its full potential and spares the operator from repeatedly purchasing new catalyst.
In processes with vertical reactors (UOP licensed process), partially deactivated catalyst is continually removed from the bottom of the reactor stack for regeneration. Side by side reactor arrangements (IFP licensed process) operates in a similar manner in that the partially deactivated catalyst is removed from the last reactor for regeneration. The regeneration process exposes the catalyst to hot air, which burns the coke off of its surface. The regenerated catalyst is then reduced, acidified and lifted with hydrogen and/or nitrogen gas back to the top of the reactor stack. In this process, an individual piece of catalyst is regenerated every three days.
There are a number of critical valves in this service. Figure 2 shows a schematic of one type of process showing the critical valves. The first valve controls the amount of catalyst from the last reactor to the lockhopper or storage tank. From the lockhopper, the flow to the regeneration section must also be controlled by another valve. Because the catalyst is very fine, the valve must be able pass the catalyst and be able to operate in cases where dust may collect on the valve trim. Fisher has developed several valves specifically for this service.
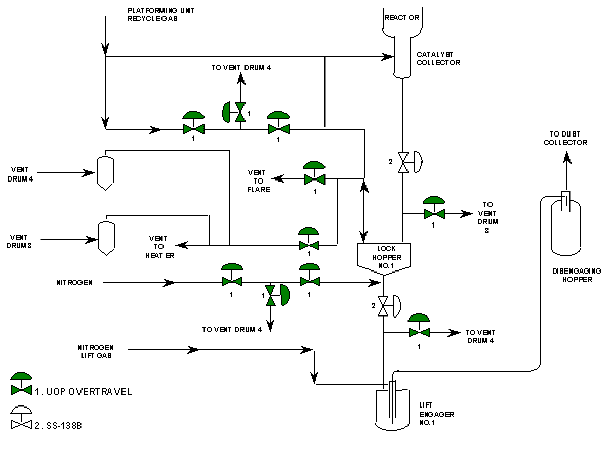
Figure 2: Catalytic Regeneration Process Flow Diagram
Several variations of the Vee-Ball line have been used with proven success in these applications. The Fisher SS-138B Vee-Ball was developed for processes that operate under atmospheric conditions. The SS-V252 was developed for pressurized units where bi-directional shutoff is required. Both solutions have specially designed flow passages to eliminate solids accumulation that can hinder valve performance.
Another set of applications that present a challenge are valves in the nitrogen and hydrogen lines that carry the spent catalyst to the regenerator and eventually to the reactor. Most of the valves used in this service are on/off vent and isolation valves that protect the system from overpressure and prevent the lost of hydrogen in the system. The valves in this service have presented repeated maintenance issues because of the entrained catalyst fines. The fines can cause issues with leakage and can eventually cause the valve trim to bind.
To address the requirements for this application, Fisher developed the EZ-OVT or over-travel valve. This dual seated valve is designed to maintain long-term bubble tight shutoff in services that have entrained particulate. In applications where the EZ-OVT has replaced existing valves, valve service life has increased by two to three times.
By utilizing a continuous catalyst regeneration process, the need to continually shutdown the reactor for regeneration is eliminated. However, the continuous operation is dependent upon a number of severe service control valves. The solutions that Fisher provides for these applications address the severe nature of the application and have been proven by field operation. |